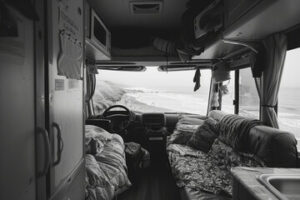
Many neighborhoods have covenants that prevent homeowners from storing their RVs on their property. And even if they do, the RV may take up space that could be used for other things like a car or lawnmower.
Dedicated RV storage facilities can provide great value for a minimal investment. Ask about pricing structures and contract terms to make sure you’re getting the best possible deal. Visit https://www.storagebayok.com/ to learn more.
1. Convenience
RVs and boats can be difficult to store at home. They are large, cumbersome vehicles that can take up valuable space in driveways and detract from curb appeal. Plus, many communities have restrictions on storing these types of vehicles at homes. This is where a good RV storage facility can help.
A RV storage facility can provide a convenient place for owners to store their recreational vehicles, whether they are not in use or need to be moved out of the way to allow for maintenance and repair work to be done on the vehicle. It can also be a cost-effective alternative to keeping an RV or boat in the garage at home, where it can become hot and humid during the summer and cold and damp during the winter.
Many RV storage facilities offer different options for storing an owner’s recreational vehicle, including indoor, covered, and outdoor storage spaces. Some facilities offer climate control, which costs more than standard storage but protects the RV from damage caused by weather extremes. Some facilities even offer electrical hookups, dump stations, and wash areas.
Another benefit of RV storage is that it can save an owner money on expensive repairs and cleaning. The RV storage can protect the vehicle from rust and corrosion, and prevent it from becoming a nesting ground for outdoor critters such as squirrels, packrats, birds, raccoons and skunks.
For investors, the RV storage market offers a great opportunity. This type of investment is less competitive than residential or commercial real estate, and it can be easier to secure a loan for development. However, it is important to thoroughly research the market to ensure that you are providing a high-demand product and that the location is suitable for RV storage (check with local planning and zoning departments and HOAs). It is also vital to understand what amenities are in demand and how much they might cost to build and operate.
2. Security
RV storage is an investment, so it makes sense to protect it with the latest security measures. A reputable RV storage facility should have video surveillance to deter crime and provide around-the-clock monitoring of each vehicle in their care. In addition to this, a good system will have entry sensors and alarms that can be activated by motion detectors, which will alert you or the local authorities to break-ins and other threats.
The biggest benefit of RV storage is that it protects your vehicles from theft and vandalism. RVs are attractive targets for thieves because they’re like homes on wheels and contain valuable items, and motorhomes are usually parked in areas with high crime rates.
Storing your RV at home leaves it vulnerable to burglary and other threats, so it’s best to store it off-site. In addition to protecting your RV from theft, RV storage facilities also take up less space at your property, freeing up room for other uses like regular vehicles, outdoor equipment, or landscaping.
Many RV storage facilities have gated access, security cameras, and on-site managers to keep an eye on each facility at all times. This provides peace of mind for RV owners, who can rest easy knowing their vehicles are being protected and their belongings are safe.
Managing an RV storage business requires a lot of time, effort, and energy. But advancements in tech integration make it easier than ever to run a facility, with rental processing, administration, and customer service able to be handled from anywhere. With proper planning and management, an RV storage business can be a lucrative and rewarding venture. And with all the new companies offering keyless locks, remote monitoring, and other tech-integrated solutions, it’s never been a better time to jump in!
3. Insurance
While your RV is parked at an RV storage facility, it’s important to keep it insured. This may seem like a waste of money, but RV insurance is an inexpensive investment that gives you peace of mind in case something unfortunate happens while your home on wheels isn’t being used.
Storing your RV at home leaves it vulnerable to theft and vandalism from neighbors or passersby, while a reputable storage facility offers a safe place for you to park your vehicle for months at a time. Thefts are common, especially in larger vehicles, and can be devastating for your financial health.
In addition to theft protection, RV storage insurance can also provide coverage in the event of severe weather or accidental collisions with other vehicles parked nearby. This kind of damage can be costly to repair or replace, but fortunately, RV insurance policies cover the majority of these expenses so that your dreams on the road aren’t put on hold.
Most RV owners have a lot invested in their home on wheels, so they don’t want to put any portion of it at risk. For this reason, many of our customers maintain full coverage on their RVs at all times.
To get more information on RV storage insurance or to discuss any other insurance related matter, contact Kinowski Agency Inc serving the Amsterdam NY area today. We would be happy to speak with you and help you find the right solution for your needs. Our experienced advisors are ready to talk where and when it’s most convenient for you. We offer convenience, value and superior customer service. You can expect to be treated with respect and care throughout the entire process, and your coverage will be customized to meet your specific needs.
4. Climate Control
Unlike your home, your RV has a lot of different components that work together to control its climate. Understanding how to use the thermostat and other systems is crucial for enjoying a comfortable trip. If you’re planning on using the system, make sure to read and follow all manufacturer instructions. These typically include ensuring that the air filter is clean and properly seated. Additionally, it’s a good idea to keep the gas tank full and add fuel stabilizer as well. This will help prevent condensation and reduce the risk of the fuel lines or water heater developing rust over time.
On hot days, to quickly cool the RV, close all the vents in the bedroom and living areas, and crank up both air conditioners. This will help to draw the air out of the rear of the RV and into the front, helping to cool the area faster. It’s also a good idea to open windows across from each other to create a cross breeze and help the cooling process along.
Aside from the RV’s built-in thermostat, some owners opt to use portable thermostats and fans that can be plugged in and controlled through a mobile app. This allows the user to check on their RV and set temperature preferences while traveling. It can also be a useful tool for determining when it’s time to replace the air filters and other parts in your RV.
For a comfortable winter trip, an RV owner should invest in some body warmers or electric blankets to stay warm. While these do require electricity to operate, they’re not very power-hungry and can be used in conjunction with the RV’s propane furnace.
5. Value
RV storage is a great addition to an existing self-storage facility and provides a lucrative new revenue stream. RV owners are willing to pay a premium for the safety and security that comes with storing their expensive vehicles in a professionally operated building, rather than leaving them on their own properties. A reputable RV storage business can generate high revenue with little startup cost and minimal management responsibilities, resulting in a low risk investment with significant upside potential.
In addition to the higher rental rates, a well-run RV storage business can increase its value by providing additional amenities that differentiate it from competitors. For example, a RV storage business could offer premium RV parking on a private lot with paved parking spaces and full hookups for electricity and water. This type of specialized parking will appeal to a specific market segment and help a property owner attract more tenants, drive up rents, and increase the overall value of the asset.
Another way to add value is by offering conveniences like a wash bay, tire pump, and a vehicle detailing service. These amenities will increase a property’s value by making it easier for customers to maintain their vehicles.
Lastly, RV storage facilities often benefit from economies of scale and have lower vacancy costs than other types of real estate. For example, the cost of painting steel canopies is much cheaper when you paint 100 units than it is when you paint only 10. This can significantly reduce a facility’s operating expenses and improve the profitability of the investment.
As the popularity of recreational vehicles and toys continues to grow, now is an excellent time to invest in a boat and RV storage facility. If you’re interested in learning more about this growing market, contact Storelocal to schedule a members-only virtual call with RV Storage Depot CEO Scott Ramser.